一、工业自动化实训设备:为何成为刚需?
随着智能工厂、柔性生产线等概念的落地,工业机器人、PLC(可编程逻辑控制器)、传感器等自动化设备已成为现代制造业的“标配”。然而,传统教育模式中“重理论、轻实践”的短板,导致大量毕业生与企业实际需求脱节。
工业自动化实训设备的出现,恰好解决了这一矛盾。通过模拟真实产线环境、集成主流技术模块,这类设备能让学生在安全可控的场景中掌握设备调试、故障诊断、系统集成等核心技能。例如,某高职院校引入PLC与工业机器人联调实训台后,学生就业率提升27%,企业满意度增长35%。
二、核心技术解析:实训设备的“硬核”构成
一套优质的工业自动化实训设备,需兼顾技术前瞻性与教学适配性。其核心模块通常包括:
PLC控制单元:作为自动化系统的“大脑”,支持西门子、三菱等主流品牌编程,培养学生逻辑控制与程序优化能力。
工业机器人模块:搭载六轴机械臂或协作机器人,模拟焊接、码垛等真实作业场景。
传感器与执行机构:涵盖光电、温度、压力等多种传感器,搭配气动元件、伺服电机,构建闭环控制链路。
人机交互界面(HMI):通过触摸屏或SCADA系统,训练学生数据监控与可视化操作能力。
以某品牌“智能制造柔性生产线实训平台”为例,其整合了AGV小车、RFID物料识别、MES系统接口,高度还原数字化工厂的运作流程,助力学生掌握工业4.0全链条技术。
DB-JQR19 工业机器人自动化综合实训平台
工业机器人自动化综合实训平台主要用于工业机器人电气系统、气动系统的设计、安装、调试、维护维修;工业机器人PLC编程;工业机器人变频、伺服系统的参数调整与编程控制;工业机器人传感器的检测与应用;人机界面编程与应用。
工业机器人自动化综合实训平台为模块化开放式设计结构,主模块可作为独立的实训系统单独使用,也可通过标准接口与电工实操、电气控制、气动控制、伺服步进、传感检测、机械拆装等子模块组合,构成不同功能的自动化控制实训项目。各种电气元器件、机械构部件、系统运行状态具有直观性,功能具有可扩展性,应用具有安全性。
工业机器人自动化综合实训平台可用于自动化电气部件、气动部件、伺服电机、步进电机、变频器、传感器、可编程控制器、触摸屏等工业控制系统中常用的设备的安装、接线、调试,可开展自动化相关控制技术的实训。
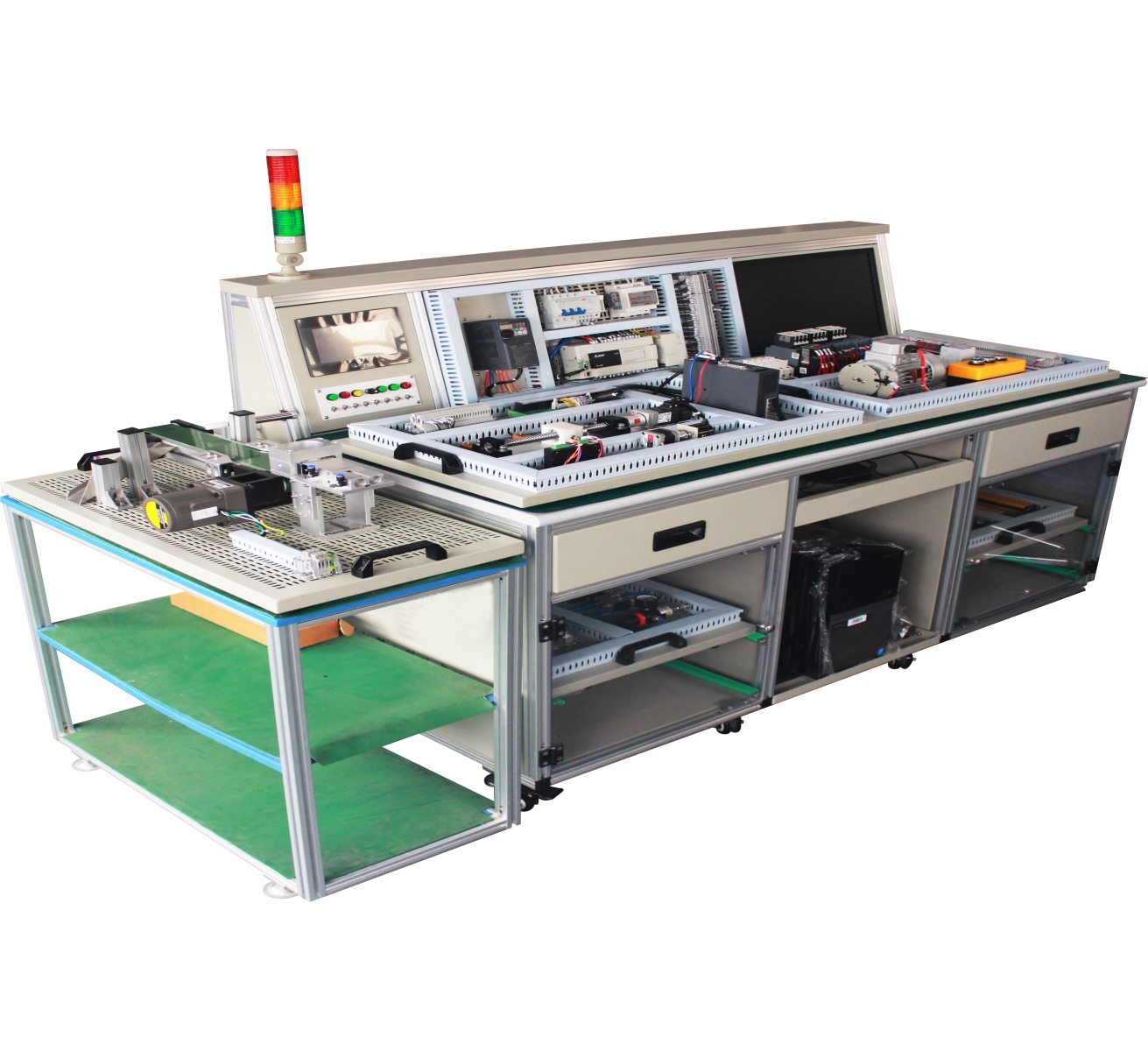
1. 院校教育:破解“纸上谈兵”困局
职业院校通过引入模块化实训设备,可将抽象的控制理论转化为具象的实操任务。例如,在“自动灌装生产线”实训项目中,学生需完成从传感器校准到整线联调的全流程,极大提升问题解决能力。
2. 企业内训:缩短员工成长周期
面对设备升级或新产线投用,企业可利用实训平台开展针对性培训。某汽车零部件厂商使用虚拟调试系统,将设备故障率降低了40%,同时将员工培训周期从3个月压缩至6周。
3. 技能竞赛:选拔行业顶尖人才
全国职业院校技能大赛、“一带一路”国际技能竞赛等赛事,均将工业自动化系统集成设为赛项。参赛选手需在限定时间内完成复杂系统的搭建与优化,充分检验其技术功底与应变能力。
四、选型指南:如何匹配实际需求?
面对市场上琳琅满目的实训设备,用户需从以下维度综合评估:
需求匹配度:明确培养目标(如侧重于PLC编程还是机器人维护),选择功能模块可扩展的设备。
技术先进性:优先支持Ethernet/IP、Profinet等工业通信协议,兼容数字孪生、边缘计算等新兴技术。
安全与易用性:配备急停按钮、防护罩等安全设计,同时提供阶梯式教学案例库,降低入门门槛。
厂商服务能力:考察售后培训、软件升级支持,避免设备因技术迭代沦为“摆设”。
某职业技术学院的经验表明,采用“基础模块+可选套件”的配置方案,既能满足多专业共享需求,又能根据预算灵活升级,性价比显著提升。
五、未来趋势:智能化与虚拟化的融合
随着AR/VR、数字孪生技术的普及,工业自动化实训正迈向“虚实结合”的新阶段。例如,通过数字孪生平台,学生可在虚拟环境中模拟设备拆装、参数调试,再切换到物理设备验证结果。这种方式不仅降低实训成本,还能突破空间限制,实现远程协作学习。
与此同时,AI技术的融入让实训设备更具“智慧”。例如,某实训系统能根据学生的操作记录,自动生成个性化学习路径,并推送薄弱环节的强化训练项目。